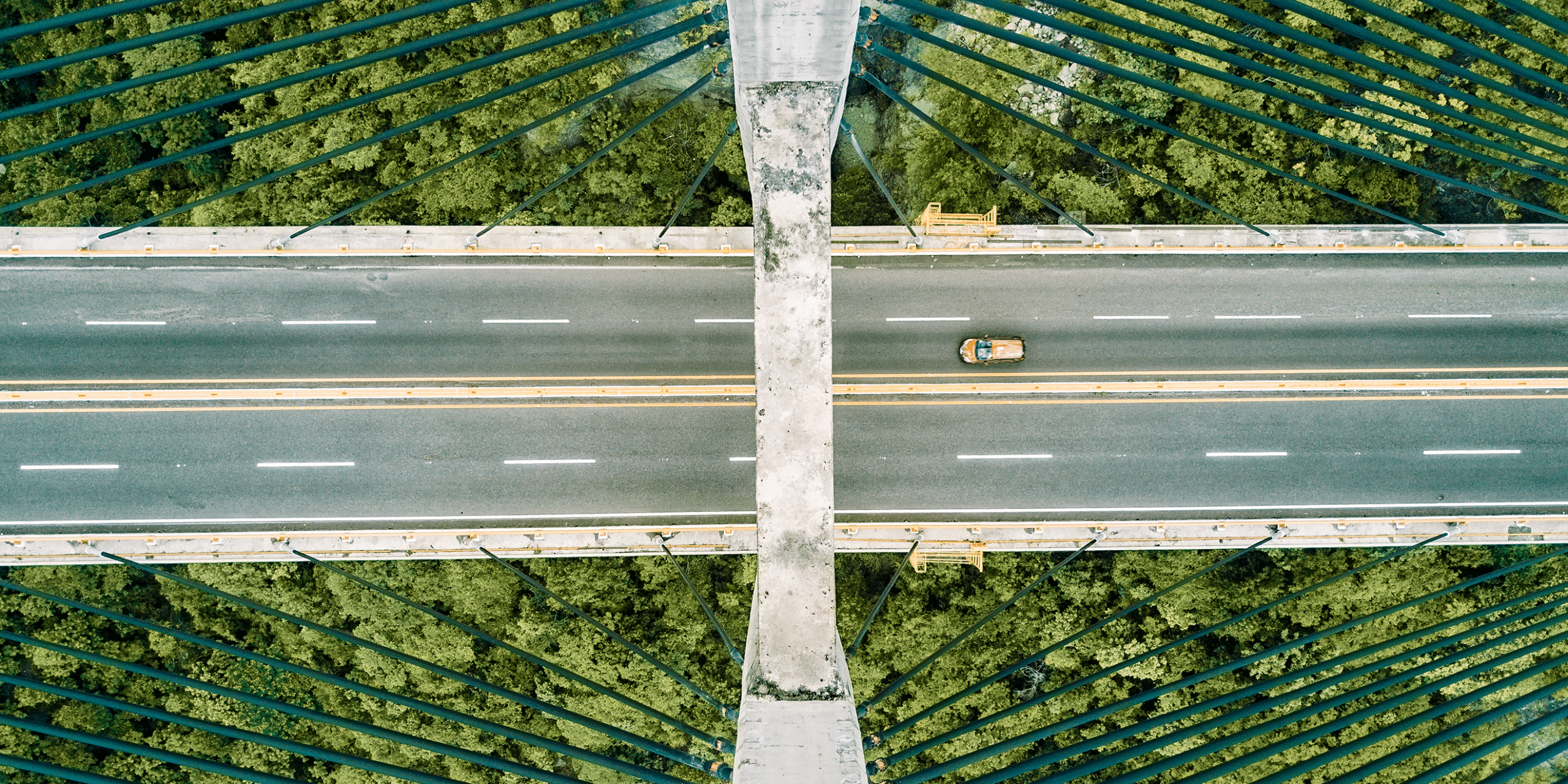
The US Department of Energy (DOE) has identified cement production as a crucial lever for decarbonizing the industrial sector in its Industrial Decarbonization Roadmap. Concrete is the most widely consumed man-made material and the production of cement, a key ingredient in concrete, is responsible for approximately 8% of global CO2 emissions. The cement production process involves heating limestone to high temperatures, releasing large amounts of carbon dioxide both from the heat required for these kilns and by the CO2 released when limestone decomposes.
The market for low-carbon alternatives to traditional cement is rapidly evolving, as construction industry groups, governments, and private sector organizations seek more sustainable solutions. This growing demand is driven by increasing regulatory pressures, corporate sustainability commitments, and a heightened awareness of the need to reduce the built environment’s carbon footprint. While these alternatives may have higher initial costs, the long-term environmental and economic benefits are promoting wider adoption. Numerous innovative options are now available for companies committed to cement and concrete decarbonization.
Current challenges and concerns
Ordinary Portland cement (OPC), the most widely used type of cement, was developed in the early 1800s and is comprised of a mixture of calcium silicates and other compounds derived from limestone and silica sources. Acting as a binder, cement is mixed with water and aggregates, like sand and gravel, to produce concrete. The cement mixture – ‘the glue’ – in concrete is called clinker. Despite making up about 10-15% of the finished concrete product’s mass, cement is responsible for 85-90% of its emissions.
Concrete has been a primary building material for centuries and is revered for its strength, resilience, and cost effectiveness. Currently, the global annual average for concrete use is roughly 30 billion tons – three times more than was the case 40 years ago. According to the Industrial Analytics Platform, demand for cement and concrete is expected to increase by more than one-third by 2050.
All of this production to meet global demand has come with a consequence – an enormous carbon footprint. OPC is an emissions-intensive material with a complex value chain and two major sources of emissions generation:
- Production Process Emissions: The chemical processes involved in producing cement, particularly the calcination process, release substantial amounts of CO2 as limestone breaks down.
- Industrial Heat Emissions: The need for continuous high-temperature heat (around 3,000 degrees Fahrenheit) to produce cement requires a huge amount of energy, much of which is still dependent on fossil fuels, like coal.
The environmental impact of OPC extends beyond production, as concrete structures also contribute to urban heat islands and other ecological disruptions. Realistically, cement emissions cannot grow linearly if the sector is to remain on track for Paris-aligned decarbonization goals.
Emerging solutions
There are numerous solutions being developed to reduce cement and concrete emissions, including low carbon concrete, clinker substitution (concrete blends), alternative production methods, and post-combustion direct air capture (DAC).
Carbon capture utilization and storage (CCUS) within concrete is a key alternative becoming more prevalent in the market. Major companies like Amazon and Microsoft are already deploying carbon utilization in concrete technology at some of their data center locations. Curing concrete by injecting and mineralizing carbon dioxide offers a way to store carbon molecules effectively, while lowering the carbon intensity of key ingredients in concrete. As the CO2 mineralizes, it becomes permanently embedded in the concrete, preventing it from reentering the atmosphere.
Mineralization can also occur by using steel slag, an often-landfilled by-product of steel manufacturing, as a replacement for Portland cement. This slag-based material differs from cement in that it does not cure by hydration, but instead by subjecting it to carbon dioxide. There are also methods like innovative powder additives that increase mineralization rates in concrete and in some cases also replace a portion of the OPC needed in the concrete mix.
Material substitution, involving the use of supplementary cementitious materials (SCMs) or alternative cementitious materials (ACMs) to replace clinker, is another effective strategy to reduce concrete emissions. According to the DOE, clinker substitution to create blended cement is the most powerful near-term decarbonization lever for concrete, one that if scaled and deployed in this decade could reduce U.S. cement emissions by 20% to 25%. As discussed earlier, steel slag or other industrial waste by-products can be used as clinker substitutes or replace cement altogether. Heated local clays are also potentially viable replacements that would reduce the amount of clinker used. Fly ash has historically been the most well-known clinker substitute, however, has received criticism because of its association with burning coal, resulting in only a marginal reduction in emissions. Material substitution offers many benefits, such as increasing the strength of the final product, reducing overall cost, and using less raw material extraction, due to its innovative use of commonly found materials or waste byproducts.
Alternative production methods such as using biomass or hydrogen instead of fossil fuels to power the production process or avoiding the use of limestone as the raw feedstock in cement are also being explored. Some technologies use electrochemical processes or lower temperature kilns to decompose calcium-bearing minerals and create alternative cements that can be used as direct replacements for OPC. Because these processes can run on renewable electricity and avoid the use of limestone as a key ingredient, they can eliminate both of the primary sources of OPC’s emissions. The DOE cites alternative binder chemistries as an important emerging technology in the market.
Using post-combustion DAC at cement plants is one of the most comprehensive mitigation options for Portland cement and one that both the Intergovernmental Panel on Climate Change (IPCC) and the Global Cement and Concrete Association (GCCA) cite as a critical mitigation option for the cement sector. The GCCA stated that carbon capture and storage (CCS) could result in roughly 36% of the concrete emissions reductions needed. Carbon utilization in the form of CO2 injection could also play a valuable role in the cement industry’s initial transition process.
Other viable solutions to solving for concrete emissions include demand management using market creation and circular economy principles, energy efficiency retrofits and initiatives, and increasing the precision of materials needs.
Opportunities for Involvement
Decarbonizing concrete is one of the defining challenges of our century that must be addressed. Companies can make a significant impact by using their resources to engage with low-carbon solutions. Supporting or deploying one of the many available solutions in the market can be an important scope 3 reduction lever for organizations. Companies seeking these sorts of value chain reductions can work with suppliers, architects, and engineers to specify low carbon concrete in building projects, and establish themselves as early adopters of new technologies.
Companies can also accelerate progress by providing funding and resources to research and development initiatives aimed at creating sustainable cement alternatives like the ones aforementioned, or by investing in or partnering with carbon project developers. Additionally, companies can purchase supply chain reductions (SCRs), carbon credits and/or invest upfront in new projects, with a commitment to forward purchase the environmental attributes. Supporting early stage low carbon cement with advanced market commitment helps startups drive down the green premium of their product and can help to unlock financing to scale and grow their facilities.
This level of support can advance climate startups from the pilot program stage to commercial viability. Organizations can drive change by implementing purchase guidelines for green cement and advocating for green public procurement commitments in major municipalities and among importers of construction materials. Companies can leverage collective purchase power to catalyze a thriving market for low-carbon cement alternatives. Lastly, corporations can use their networks to collaborate with other companies, industry groups, and academic institutions to share best practices, learnings, and promote widespread adoption of lower carbon standards.
Take action now
To decarbonize the emission-intensive production of cement, market creation and support are needed to spur efforts toward net zero. While numerous solutions are available and continuously emerging, much work remains to reach scalable deployment. Early climate action can lead to significant reductions in GHG emissions and put you on track to meet upcoming guidance and regulations. Proactive sustainability efforts can also result in long term cost savings. By raising awareness, investing in innovation, and supporting policy changes, corporations can lead the way in decarbonizing concrete and contributing to a cleaner future.
3Degrees specializes in developing supply chain carbon reduction and removal projects, and is an active partner to numerous low-carbon concrete startups. Learn more about how your organization can support these vital emission reduction technologies by getting in touch today.
Speak to a carbon advisor
3Degrees specializes in developing supply chain carbon reduction and removal projects, and is an active partner to numerous low-carbon concrete startups. Learn more about how your organization can support these vital emission reduction technologies.
Suggested insights
Explore more of our latest climate insights.